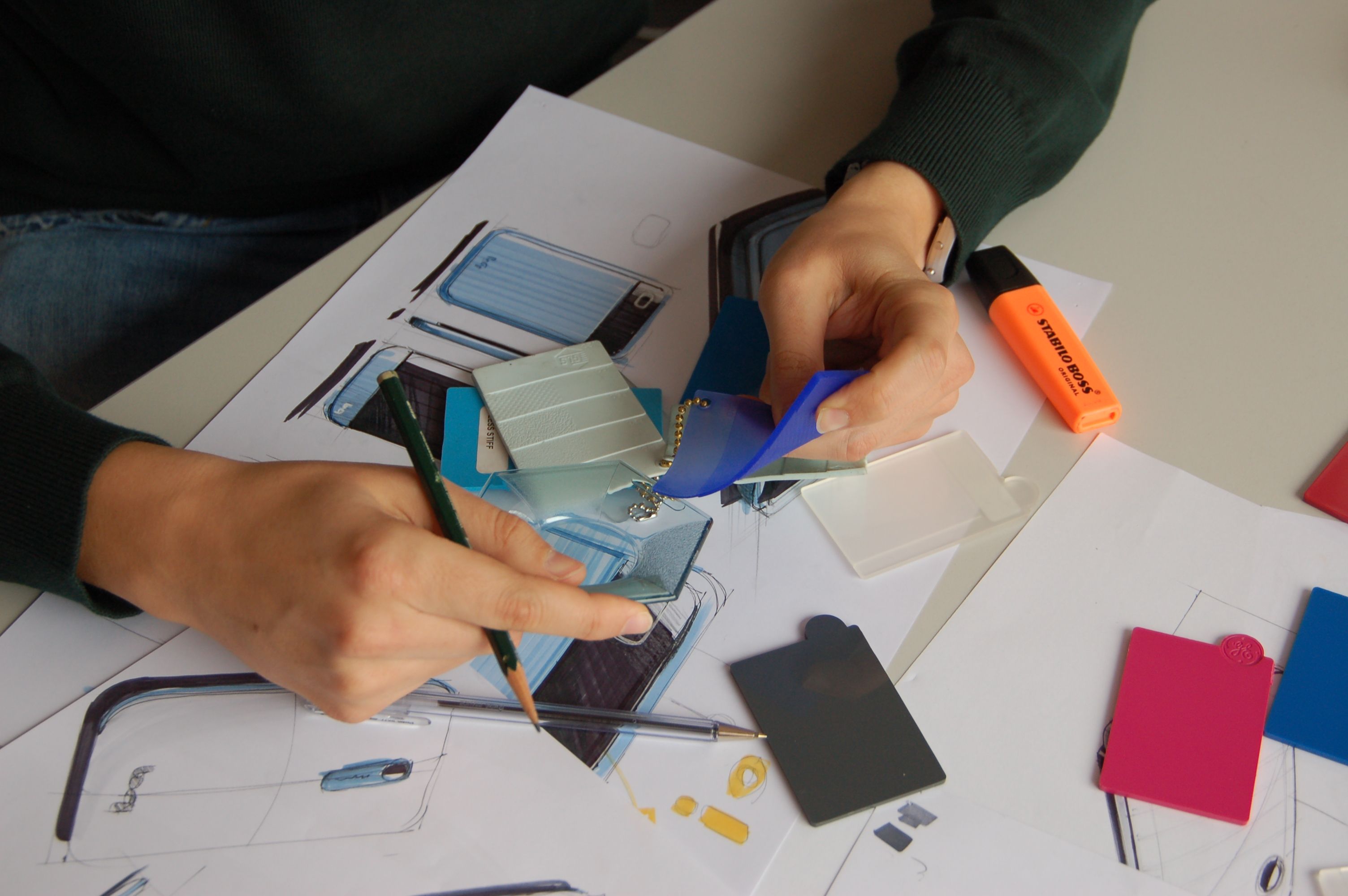
Often many companies think that any product concept can be manufactured. Actually they are not wrong; almost everything can be manufactured, but it always depends on the budget and the deadline. As we all know these are the biggest restrictions in the project development.
When we address the task of presenting a new concept we need to consider functionality, color and material trends, ergonomics and form, and other small details that eventually define the product personality.
But be careful, we cannot forget that it needs to be manufactured: we want to sell “X” thousands of units during a certain lifecycle and under an unavoidable tight budget. For this reason, it is essential to work hand-in-hand with designers, engineers, and material and trend experts in the new product development process in order to ensure the excellence of the product in every detail.
A key aspect that must be defined carefully before starting to design is the manufacturing cost limit. Having this exact information we can start thinking about different processes, number of parts, assembly and material families, amongst many others.
Let’s take the design of a mobile phone as example. In the definition of the shell, mechanized aluminum and posterior polishing don”t cost the same price as injected plastic and IMD post-process (“in mold decoration”) to give a metallic appearance or injected plastic directly with the final color. If we consider that our budget fits the plastic injection with the final color and protection coating, then we can consider the number of parts that we can include in the ensemble. Each part implies tools, development and maintenance costs to take into account.
The composition material is an essential parameter in the perception of the product. If we have clearly defined the type of material that our mobile phone needs, injection plastic in this case, we can consider the type of plastics that perform better for this application. The plastic world is really broad and it is fast moving industry with frequent innovations: bioplastics, autofixable plastics, high mechanical performance, UV radiation resistant, TPU anti-static, etc. It is important to be up-to-date with materials, properties, manufacturers and applications to use them creatively. In certain cases, an unexpected material might work perfectly in the new product.
The definition of the material is crucial; it contributes to the product”s perceived quality, the feelings of the user while touching and looking at it, and product ageing. Following on from the mobile phone example, we have decided to use injected plastic for the shell; hence we need to select a high quality finishing material that is UV radiation resistant and a material that avoids injection marks. For example, if we select a PP with internal fibers, we will have a disappointing surprise in the moment of injection because these fibers will appear in the surface drawing the path that they follow when entering the mold. Therefore, it is vital to thoroughly study, with the supplier, the injection process of the object and the color range that can be achieved.
This has just been a brief glance at the topic. Many other aspects needs to be analyzed when designing a product. This is not a rigid and closed process. It is flexible and varies in each case depending on the type of project. Product conceptualization demands a certain material, while others focus on a fixed cost that cannot be surpassed. It is our task to creatively apply of our expertise to satisfy the requirements of our clients in order to deliver a relevant product which do not disappoint the end users.
Let’s grow together!
Have questions about your next growth move?
Mormedi has answers.